Pumps play a vital role in various industries, facilitating the movement of fluids and ensuring efficient operations. The selection of the right pump for a specific application is crucial for optimal performance. Two common types of pumps are end suction pumps and inline pumps. In this article, we will delve into the characteristics, applications, advantages, and limitations of both types, providing insights to help you make an informed decision.
End Suction Pump
An end suction pump, as the name suggests, has an inlet located at one end of the casing. It uses an impeller to create centrifugal force, which draws fluid into the casing and then pushes it out through the discharge port. The pump is typically mounted horizontally and is designed for medium to high flow rates.
Construction and Design Features:
End suction pumps are typically single-stage, with a simple construction that consists of a casing, impeller, shaft, and bearings. The casing is often designed with flanges for easy installation and maintenance. These pumps can be made of various materials, such as cast iron, stainless steel, or bronze, depending on the application requirements.
Applications and Industries:
End suction pumps find wide application across industries, including water supply and distribution, HVAC systems, irrigation, general industrial processes, and wastewater treatment. Their ability to handle large volumes of fluids makes them suitable for applications that require high flow rates.
Advantages of End Suction Pumps:
End suction pumps offer several advantages, including:
- Simple installation and maintenance due to their straightforward design.
- Cost-effectiveness, as they are often less expensive compared to other pump types.
- Versatility, with the ability to handle various fluids and temperatures.
- Wide availability in the market, with a range of sizes and configurations to meet diverse needs.
Limitations and Considerations:
Despite their benefits, end suction pumps have a few limitations to consider:
- Limited head capabilities compared to other pump types, making them unsuitable for high-pressure applications.
- Reduced efficiency at lower flow rates, which can lead to increased energy consumption in certain scenarios.
- Potential issues with cavitation if not properly sized or operated.
Inline Pump
An inline pump, also known as a close-coupled pump, is designed to have a compact and space-saving configuration. It operates by drawing fluid in through an inlet and discharging it through an outlet in a single straight line. Inline pumps are typically used for low to medium flow rates.
Construction and Design Features: Inline pumps have a compact design, with the motor directly coupled to the pump impeller. This eliminates the need for a separate coupling or alignment. The pump and motor assembly is usually mounted on a common baseplate, simplifying installation and reducing footprint.
Applications and Industries:
Inline pumps are commonly used in applications such as water circulation, heating and cooling systems, booster systems, and industrial processes that require moderate flow rates and relatively low pressures.
Advantages of Inline Pumps:
Inline pumps offer several advantages, including:
- Space efficiency, as they require less floor space due to their compact design.
- Ease of installation and maintenance, thanks to their integrated motor and simplified assembly.
- High operational efficiency, especially at lower flow rates.
- Reduced risk of cavitation due to the straight-through design.
Limitations and Considerations:
While inline pumps have their benefits, it’s important to consider the following limitations:
- Limited to moderate pressure capabilities, making them unsuitable for high-pressure applications.
- Higher initial cost compared to end suction pumps.
Comparison between End Suction and Inline Pumps:
Performance Characteristics:
When comparing end suction pumps and inline pumps, it’s important to consider their performance characteristics:
- Flow Rate: End suction pumps are better suited for high flow rate applications, while inline pumps are more suitable for moderate flow rates.
- Head and Pressure: End suction pumps are capable of handling higher head and pressure requirements compared to inline pumps.
- Efficiency: Inline pumps tend to exhibit higher efficiency at lower flow rates, while end suction pumps may experience reduced efficiency in such scenarios.
Installation and Space Requirements:
End suction pumps typically require more space due to their horizontal configuration and the need for additional components like couplings. On the other hand, inline pumps have a compact design, requiring less floor space and simplified installation.
Maintenance and Accessibility:
Both end suction and inline pumps offer ease of maintenance, but their accessibility may differ. End suction pumps may require more effort to access internal components due to their larger size, while inline pumps provide better access due to their compact design.
Cost Considerations:
End suction pumps are generally more cost-effective upfront, as they are often less expensive and readily available in various sizes and configurations. Inline pumps may have a higher initial cost due to their integrated motor and compact design.
Selection Factors Based on Application Requirements:
The selection between end suction and inline pumps ultimately depends on the specific application requirements. Factors to consider include flow rate, head and pressure requirements, available space, installation constraints, maintenance accessibility, efficiency expectations, and budget considerations. Consulting with pump experts and considering the long-term operational costs can aid in making the most suitable choice.
Conclusion:
Choosing between end suction pumps and inline pumps requires careful consideration of various factors. End suction pumps excel in high flow rate applications, offer simplicity and versatility, but have limitations in terms of head capabilities and efficiency at lower flow rates. Inline pumps, on the other hand, are compact, space-efficient, and offer high efficiency at lower flow rates, but may have limitations in handling high pressures. By evaluating the specific requirements of your application and considering the advantages and limitations of each pump type, you can make an informed decision that ensures optimal performance and cost-effectiveness. Seeking guidance from pump experts is recommended to select the most suitable pump for your specific needs.
Recent Posts
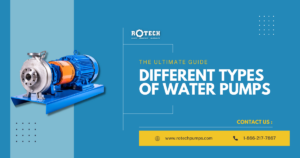
A Comprehensive Guide to Types of Water Pumps and Their Applications
Introduction Water pumps are indispensable
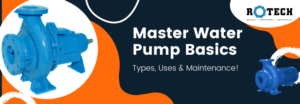
The Complete Guide to Water Pumps: Types, Uses, and Maintenance
Water is life, and the
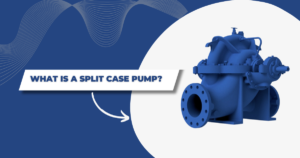
Comprehensive Guide to Split Case Pumps
Split case pumps are a