I. Introduction to Pumps in the Food Industry
Pumps are indispensable in the food processing sector, facilitating the movement of liquids, semi-solids, and solids throughout various stages of production. Selection of appropriate pumps is crucial, considering factors like compliance with stringent hygiene standards, adherence to FDA regulations governing food-grade equipment, and the necessity to maintain uncompromised food safety.
II. Classification of Pumps Based on Operating Principles
A. Positive Displacement Pumps
1. Rotary Pumps:
a. Gear Pumps:
Gear pumps operate by using rotating gears to move fluids through the pump. These pumps are highly reliable and suitable for handling viscous food substances such as chocolate, syrups, and oils without causing damage or altering their properties.
b. Lobe Pumps:
Lobe pumps gently handle shear-sensitive food products, making them perfect for transferring delicate substances like dairy, cosmetics, and certain pharmaceuticals.
c. Peristaltic Pumps:
With a unique design utilizing rollers compressing a flexible tube, peristaltic pumps are excellent for pumping shear-sensitive and abrasive fluids without contamination risks. They are commonly employed in the transfer of fruit juices, sauces, and pharmaceutical formulations.
2. Reciprocating Pumps:
a. Piston Pumps:
Piston pumps are highly efficient in handling high-pressure applications such as food pastes, sauces, and creams. They offer precise control over the flow rate and are suitable for metered dosing.
b. Diaphragm Pumps:
These pumps are ideal for transferring food substances without exposing them to external contaminants. Diaphragm pumps are commonly used in pharmaceuticals and food industries where product purity is critical.
B. Dynamic Pumps
a. Single-stage Centrifugal Pumps:
These pumps are well-suited for transferring low-viscosity fluids like fruit juices, milk, and other beverages in food processing plants. They’re commonly used in the initial stages of production lines.
b. Multi-stage Centrifugal Pumps:
Multi-stage centrifugal pumps are designed for higher pressure applications like pasteurization, high-pressure cleaning systems, and in systems requiring a significant boost in pressure for conveying liquids.
2. Other Dynamic Pumps:
a. Axial Flow Pumps:
Axial flow pumps are suitable for transporting large volumes of fluids, making them essential in industries like breweries and wineries where bulk liquid movement is necessary.
b. Mixed Flow Pumps:
Mixed flow pumps are utilized for handling mixtures of solids and liquids in food processing, ensuring efficient and reliable transport of such mixtures without clogging or damage to the pump components.
III. Application-specific Considerations for Food Processing
A. Pump Materials and Construction
1. Stainless Steel Pumps:
Stainless steel pumps are a cornerstone in food processing due to their excellent corrosion resistance and ability to maintain hygiene standards. These pumps are extensively used in dairy, brewing, and pharmaceutical applications where cleanliness and durability are paramount.
2. Sanitary Pumps:
Pumps specifically designed for the food industry prioritize easy cleaning and sterilization. Their smooth surfaces, minimal crevices, and hygienic design features ensure thorough sanitation to prevent bacterial growth and contamination risks in food products.
3. Non-metallic Pumps:
Certain food substances may react with metal, affecting product quality or taste. Non-metallic pumps, made from materials like food-grade plastics or elastomers, are employed to handle these specific food types while ensuring product integrity.
B. Pump Sealing and Containment
1. Sealing Methods:
Pumps in the food industry utilize various sealing methods, such as mechanical seals or double seals, to prevent leakage and ensure that food products remain uncontaminated during transportation.
2. Containment Strategies:
Closed-loop systems and containment measures are employed to maintain the integrity of food products, ensuring they remain isolated from external contaminants throughout the pumping process.
C. Handling Viscous and Abrasive Food Products
1. Pumps for Viscous Fluids:
In handling high-viscosity substances like pastes, creams, and sauces, pumps like lobe pumps or peristaltic pumps are chosen for their gentle handling and ability to maintain product consistency without altering properties.
2. Abrasion-resistant Pump Designs:
Pump designs using specialized materials and coatings prevent wear and tear caused by abrasive food products, enhancing pump longevity and minimizing maintenance needs in applications involving abrasive substances.
IV. Specific Types of Food Products and Corresponding Pumps
A. Liquid Foods
1. Dairy Products:
Pumps used in dairy applications must meet stringent cleanliness standards. For instance, in milk handling, sanitary positive displacement pumps are often preferred due to their gentle handling of the product and the ability to maintain hygiene during transfer.
2. Beverages:
In the beverage industry, pumps play a crucial role in transferring various liquids like juices, concentrates, and syrups. Centrifugal pumps are commonly employed for their efficiency in handling low-viscosity fluids, ensuring the preservation of product quality.
3. Sauces and Dressings:
When dealing with viscous substances like ketchup, mayonnaise, and salad dressings, pumps with specific capabilities to handle thick and chunky materials, such as peristaltic pumps or piston pumps, are used to maintain product integrity during transfer.
B. Solid Foods and Food Particles
1. Handling Solids in Liquids:
For food products with solid components like soups, sauces with chunks, or purees, positive displacement pumps like rotary lobe pumps or peristaltic pumps are preferred to delicately handle these mixtures without damaging the ingredients.
2. Fruits and Vegetables:
Pumps designed to handle whole or processed fruits and vegetables require durability and reliability. Depending on the specific application pumps with non-clogging capabilities, like axial flow or diaphragm pumps, are used for efficient transport without compromising product quality.
3. Meat Processing:
In meat processing facilities, pumps capable of handling ground or minced meat are utilized. These pumps should have the capacity to transport semi-solid materials efficiently, such as peristaltic or positive displacement pumps designed for handling viscous substances.
V. Hygiene and Cleanability in Food-grade Pumps
A. Cleaning-in-place (CIP) Systems
1. Integration with Pumps:
CIP systems are crucial in the food industry for maintaining cleanliness without disassembling equipment. Pumps designed for CIP integration allow thorough cleaning of internal surfaces, minimizing the risk of contamination between product runs.
B. Design for Sanitation
1. Disassembly and Sanitization:
Pumps with designs allowing easy disassembly and reassembly facilitate thorough cleaning and sanitation. Smooth surfaces, polished finishes, and minimal crevices prevent bacterial growth and ensure compliance with strict hygiene standards.
VI. Maintenance and Operational Considerations
A. Preventive Maintenance
1. Monitoring and Maintenance:
Regular monitoring and maintenance schedules are essential for sustaining pump performance. Scheduled checks, lubrication, and replacing worn-out parts prevent unexpected breakdowns and ensure continuous operation.
B. Efficiency and Energy Consumption
1. Optimizing Efficiency:
Implementing energy-efficient pumps and adopting measures such as variable frequency drives (VFDs) to adjust pump speed according to demand significantly reduces energy consumption, contributing to cost savings and environmental sustainability.
VII. Case Studies and Industry Examples
1. Real-world Applications:
Case studies showcasing successful implementations of different pump types in food processing illustrate their effectiveness in maintaining product quality and meeting industry standards. For instance, a dairy company utilizing sanitary rotary lobe pumps for gentle handling of dairy products, ensuring hygienic transfer without compromising quality.
2. Challenges Faced:
Discussing challenges encountered in integrating specific pump technologies can provide insights into the evolving needs of the food industry. For example, overcoming issues related to pump wear in processing abrasive food substances and subsequent adaptations made to enhance pump durability.
VIII. Future Trends and Innovations
A. Emerging Technologies
1. Innovative Pump Designs:
Continuous advancements in pump technology focus on improving efficiency, reliability, and hygiene. For instance, the development of self-cleaning mechanisms or innovative materials resistant to corrosion and abrasion could revolutionize pump designs for food processing applications.
2. Digitalization Impact:
Integration of smart sensors and IoT (Internet of Things) technologies into pump systems enables real-time monitoring of performance parameters. Predictive maintenance based on data analytics helps prevent breakdowns and optimize operational efficiency.
IX. Conclusion
The selection and application of pumps in the food industry are critical for maintaining product integrity, meeting hygiene standards, and ensuring operational efficiency. Understanding the diverse pump types and their specific applications in handling various food products are crucial steps toward ensuring food safety and quality.
Adhering to regulatory standards, selecting appropriate materials, implementing efficient cleaning protocols, and adopting maintenance practices significantly contribute to the reliability and effectiveness of pumps in food processing operations.
In conclusion, the continuous evolution of pump technologies, coupled with adherence to stringent hygiene practices and innovative solutions, promises a future where food-grade pumps will play an increasingly integral role in ensuring the production of safe, high-quality food products.
Recent Posts
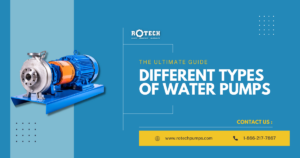
A Comprehensive Guide to Types of Water Pumps and Their Applications
Introduction Water pumps are indispensable
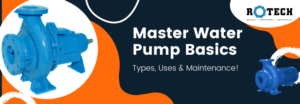
The Complete Guide to Water Pumps: Types, Uses, and Maintenance
Water is life, and the
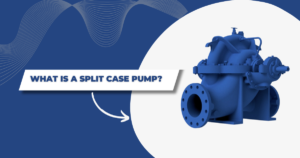
Comprehensive Guide to Split Case Pumps
Split case pumps are a