Imagine this: the heart of your production line, your trusty chemical pump, starts sputtering and coughing. Acidic ooze backs up, gears grind, and alarms blare. Panic seizes the air as seconds tick by, each one costing you thousands in lost production and potential spills.
Chemical pump failure is not just a maintenance headache, it’s a ticking time bomb. These workhorses powering everything from delicate pharmaceutical production to heavy-duty mining operations are the unsung heroes of industry. But neglect their care, and they’ll transform from loyal servants into costly saboteurs.
But fear not, fellow industrial warriors! Today, we’re not just sounding the alarm; we’re providing the defusal kit. This blog post is your ultimate guide to extending the lifespan of your chemical pumps, turning those ticking time bombs into reliable champions of production.
Within these digital pages, you’ll discover:
- The ABCs of Pump Anatomy: We’ll demystify the different types of chemical pumps and their unique needs. (Think centrifugals waltzing with gear pumps, while diaphragms tap their own steady rhythm.)
- Your Preventative Maintenance Checklist: No more guesswork! We’ll provide a clear roadmap for regular inspections, lubrication, and cleaning, ensuring your pumps purr with peak efficiency.
- Troubleshooting Tips for the Everyday Hero: Leaky seals? Wobbly impellers? We’ll equip you with the knowledge to handle common pump woes like a seasoned pro.
So, put down the wrench and grab a cup of your favorite industrial-strength coffee. It’s time to turn those ticking time bombs into ticking treasures! Dive into this blog and unlock the secrets to long-lasting pump performance, maximizing your production, minimizing your headaches, and ensuring your factory hums with the sweet symphony of uninterrupted workflow.
Remember, your pumps are the silent guardians of your success. Give them the TLC they deserve, and they’ll reward you with years of smooth, reliable operation.
Now, let’s get started!
Before we dive into the nitty-gritty of maintenance, let’s lay the foundation: understanding the different types of chemical pumps and their unique needs. Think of this as equipping yourself with a map before venturing into the jungle of pump maintenance.
1. Centrifugal Pumps: The Whirlwind Warriors:
Imagine a spinning impeller swirling liquid like a miniature hurricane. That’s the magic behind centrifugal pumps – the workhorses of the chemical pumping world. They excel at high flow rates for low- to medium-viscosity fluids, making them ideal for transferring bulk chemicals, water, and thin slurries. But remember, these whirlwinds aren’t built for solids or abrasives, so keep those out of their way!
2. Gear Pumps: The Clockwork Kings:
Precision and control are the hallmarks of gear pumps. Their intermeshing gears gently guide fluids with minimal pulsation, perfect for delicate applications like metering sensitive chemicals or transferring viscous liquids like resins and oils. However, like clockwork mechanisms, they require careful lubrication and can be susceptible to high pressures and solids.
3. Diaphragm Pumps: The Gentle Giants:
If you need a touch of finesse, turn to diaphragm pumps. These champions handle abrasive fluids and solids with ease, thanks to their flexible membranes that pulsate like beating hearts. They’re also self-priming and air-operated, making them versatile for remote locations or hazardous environments. But their flow rates tend to be lower than other types, so keep that in mind for your needs.
This is just a glimpse into the diverse world of chemical pumps. Understanding their strengths and weaknesses is the first step in providing the right care and extending their lifespan. In the next sections, we’ll explore essential maintenance practices tailored to each type, ensuring your pumps become true champions of production, not ticking time bombs waiting to explode.
Remember, knowledge is power! The more you understand your pumps, the better equipped you are to keep them purring smoothly and efficiently. So, let’s delve deeper into the world of pump maintenance and turn those ABCs into a full-fledged pump mastery course!
From Watchdog to Warrior: Your Preventative Chemical Pump Maintenance Checklist
Item | Description | Frequency | Procedure | Pass/Fail | Notes |
---|---|---|---|---|---|
Visual Inspection | Inspect for leaks, corrosion, cracks, loose parts, misalignment, and unusual noises or vibrations. | Daily | Visually examine the pump and surrounding areas. | Pass/Fail | Note any observations or concerns. |
Lubrication | Check oil levels and condition. Replenish or change oil as needed. | Weekly or per manufacturer’s recommendations | Follow manufacturer’s instructions for checking and adding oil. | Pass/Fail | Record oil levels and any actions taken. |
Alignment | Check motor and pump alignment for proper coupling. | Monthly or as needed | Use a dial indicator or laser alignment tool. | Pass/Fail | Adjust alignment if necessary. |
Vibration | Monitor vibration levels using a vibration analyzer. | Quarterly or as needed | Compare readings to baseline or acceptable limits. | Pass/Fail | Investigate and address any excessive vibration. |
Seals | Check for leaks or wear on seals. Replace as needed. | Quarterly or as needed | Inspect seals visually for signs of wear or leakage. | Pass/Fail | Note the condition of seals and any actions taken. |
Valves | Inspect valves for proper operation and seating. | Quarterly or as needed | Manually operate valves and check for smooth movement and tight closure. | Pass/Fail | Perform any necessary maintenance or repairs. |
Pressure Relief Devices | Test pressure relief devices to ensure proper operation. | Annually or as required by regulations | Follow manufacturer’s instructions for testing. | Pass/Fail | Record test results and any actions taken. |
Performance Testing | Measure flow rate, pressure, and power consumption to verify pump performance. | Annually or as needed | Use appropriate testing equipment and procedures. | Pass/Fail | Compare readings to manufacturer’s specifications and investigate any discrepancies. |
Cleaning | Clean pump internals and exterior to remove buildup of chemicals or debris. | As needed | Follow manufacturer’s instructions for cleaning methods and materials. | N/A | Note any observations or concerns. |
Record Keeping | Maintain accurate records of all maintenance activities, including dates, actions taken, and results. | Ongoing | Use a maintenance log or software system. | N/A | Ensure records are accessible for future reference and troubleshooting. |
We’ve identified the diverse cast of characters in your pumping world, now it’s time to arm them with the tools of longevity! Regular preventative maintenance is the key to transforming those ticking time bombs into dependable production warriors. Think of it as a personalized training regimen for your pumps, keeping them fit and ready to tackle any challenge.
1. Inspections – Your Eagle Eye:
Just like a superhero needs to scout the scene, regular inspections are crucial for early detection of potential problems. Develop a schedule based on your pump type and operating conditions, ideally weekly for critical operations. Keep an eagle eye out for:
- Leaks: Check around seals, packing glands, and connections for any drips or weeping. Early detection can prevent major spills and equipment damage.
- Excessive Vibration: Uncharacteristic tremors could indicate worn bearings, misalignment, or cavitation. Invest in a vibration analyzer for more sensitive measurements.
- Temperature: Hot bearings or unusual heat radiating from the pump casing can signal internal issues. Monitor operating temperatures and compare them to baseline data.
Remember, even the smallest anomaly can be a clue to deeper problems. By catching them early through regular inspections, you can nip maintenance challenges in the bud and minimize downtime.
2. Fluid Fitness – Keeping the Flow:
Just as exercise fuels our bodies, the right fluid keeps your pumps operating optimally. Here’s how to ensure they’re always hydrated:
- Matching Your Pump to the Fluid: Different pumps handle different viscosities and abrasiveness. Ensure you’re using the right pump for the job to avoid premature wear and tear.
- Filtration First Aid: Think of filters as your pump’s personal trainers, removing debris and contaminants that can clog impellers and damage seals. Choose and maintain filters based on the specific fluid characteristics.
- Monitoring the Temperature: Overheated fluids can degrade pump performance and damage components. Keep an eye on fluid temperature and implement cooling systems if necessary.
Remember, the right fluid flow is the pump’s lifeblood. By choosing the right pumps, filtering effectively, and managing temperature, you ensure smooth operation and extend your pump’s lifespan.
3. Lubrication & Sealing: Pumping Up Protection
Imagine a superhero without their trusty shield and armor. Lubrication and sealing are your pump’s equivalent, safeguarding its internal workings and ensuring smooth operation.
Lubrication – The Oil of Champions: Regular oil changes aren’t just for cars; your pumps need lubrication too! Different types require specific lubricants, so consult your manual for the right viscosity and grade. Here’s how to keep your pumps oiled up:
- Schedule Matters: Develop a lubrication schedule based on operating hours or workload. Frequent lubrication is crucial for high-demand pumps.
- Level Up!: Maintain proper oil levels according to the manufacturer’s instructions. Overfilling can cause leakage, while underfilling can lead to overheating and wear.
- Cleanliness Counts: Keep lubricant reservoirs clean and free of contaminants to prevent clogs and premature bearing failure.
Remember, proper lubrication is a silent guardian against friction and wear. By following these tips, you ensure your pumps operate smoothly and efficiently, extending their lifespan and saving you from costly repairs.
Sealing the Deal: Leak-Proof Heroes: Seals are the gatekeepers of your pump, preventing fluid leaks and protecting internal components. Choose the right material for your specific liquid and ensure they’re properly installed and inspected:
- Visual Vigilance: Regularly check for signs of wear and tear, such as cracks, tears, or hardening. Replace worn seals promptly to avoid leaks and contamination.
- Tighten Up!: Maintain proper torque on seal gland nuts to prevent leaks, but avoid overtightening, which can damage the seal.
- Leak Detection Champions: Utilize drip pans or leak detection systems to catch any early signs of leakage and prevent bigger problems.
Remember, a leak isn’t just a mess; it can indicate internal damage and compromise pump performance. By diligently monitoring and maintaining your seals, you keep your pumps leak-proof and your production flowing smoothly.
4. Storage & Cleaning: Pump Pampering for Peak Performance
Even superheroes need occasional rest and rejuvenation. When your pumps take a break, proper storage and cleaning ensure they return to action refreshed and ready to conquer.
Storage Savvy: Think of storage as your pump’s hibernation chamber, protecting it from the elements and preserving its functionality. Here’s how to tuck your pumps in for a good night’s sleep:
- Drain and Dry: Remove all fluids from the pump and piping to prevent corrosion and bacterial growth. Dry thoroughly with clean cloths or compressed air.
- Protect and Seal: Apply a light coat of rust preventative to exposed metal surfaces. Close caps and valves tightly to prevent dust and moisture ingress.
- Temperature Controlled: Avoid storing pumps in extreme temperatures or direct sunlight. A cool, dry environment is ideal for long-term preservation.
Remember, proper storage prevents rust, cracks, and other forms of degradation, ensuring your pumps are ready to spring back into action when needed.
Cleaning Champions: Just like you wouldn’t send a superhero into battle covered in grime, regular cleaning keeps your pumps functioning at their peak. Here’s how to give them a well-deserved spa treatment:
- Frequency Matters: Determine your cleaning frequency based on usage and fluid type. Pumps handling abrasive or corrosive liquids may require more frequent cleaning.
- Flush it Out: Flush the pump and piping with clean water or appropriate cleaning solutions after every use. Disassemble accessible components for thorough cleaning.
- Inspection Time: Take advantage of cleaning to inspect for wear and tear, seal conditions, and any hidden damage.
Remember, routine cleaning removes contaminants, prevents blockages, and extends your pump’s life. Think of it as an investment in their future performance and a safeguard against costly repairs.
5. Troubleshooting Tricks: When Pumps Become Puzzled:
Even the bravest heroes face challenges. But fear not, with a few troubleshooting tricks, you can transform pump breakdowns from villainous setbacks into minor skirmishes.
Leakage Woes:
- Seal Suspects: Check for worn or damaged seals and tighten gland nuts if necessary. Replace seals if leaks persist.
- Connection Conundrum: Inspect pipe connections for loose fittings or cracks. Tighten them or use leak sealant as needed.
- Internal Investigations: For persistent leaks, consult a qualified technician to diagnose internal issues.
Performance Perplexities:
- Flow Fumble: Verify proper priming, filter cleanliness, and ensure there are no blockages in the piping.
- Noise Nightmare: Excessive vibration or unusual sounds could indicate bearing issues, misalignment, or cavitation. Consult a technician for advanced troubleshooting.
- Pressure Plunge: Check for air leaks, worn impellers, or inadequate power supply. Consult the manual or a technician for further diagnosis.
Remember, most pump issues can be resolved with basic troubleshooting. These tips can help you regain control and get your pumps back to full force. However, if the problem persists, don’t hesitate to seek professional help for accurate diagnosis and repair.
Congratulations! You’ve completed your pump training, graduating from novice to pump maintenance master. But remember, even the most skilled heroes need a trusty support team. Check out these bonus resources to solidify your pump prowess:
1. Manufacturer Manuals: Consider these your pump’s instruction manuals, detailing specific maintenance schedules, lubrication recommendations, and troubleshooting guides. Keep them handy for quick reference!
2. Industry Associations and Resources: Organizations like the Hydraulic Institute and the American Pump Manufacturers Association offer valuable resources, technical guides, and training programs to deepen your pump knowledge.
3. Online Communities and Forums: Connect with fellow pump enthusiasts and experts on online platforms. Share experiences, ask questions, and learn from others facing similar pump challenges.
4. Professional Pump Maintenance Services: Remember, you don’t have to face every pump hiccup alone. Consult professional pump maintenance providers for expert diagnoses, repairs, and ongoing maintenance support.
5. Stay Informed: Keep your finger on the pulse of the pump world by subscribing to industry publications and attending relevant conferences. New technologies and best practices are always emerging, so continuous learning is key.
Remember, maintaining your chemical pumps isn’t just about preventing meltdowns; it’s about empowering them to be the heroes of your production line. With the knowledge and resources you’ve gained from this blog post, you’re well on your way to turning those ticking time bombs into champions of efficiency and productivity. So pump up your confidence, put your maintenance plan into action, and watch your pumps become the unstoppable powerhouses they were always meant to be!
Recent Posts
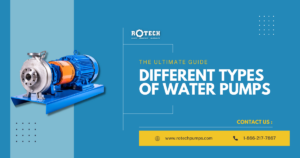
A Comprehensive Guide to Types of Water Pumps and Their Applications
Introduction Water pumps are indispensable
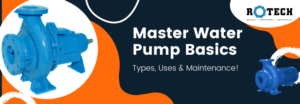
The Complete Guide to Water Pumps: Types, Uses, and Maintenance
Water is life, and the
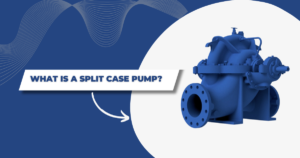
Comprehensive Guide to Split Case Pumps
Split case pumps are a