Centrifugal pump impellers are an important component of a centrifugal pump. They are used to increase the pressure and velocity of the fluid that is being pumped by a centrifugal pump.
A centrifugal pump impeller is a rotating blade with a curved shape. The blades create an increase in pressure and velocity for fluids that they are pumping by spinning them at high speeds in a circular motion. This creates a rotating helical flow which forces the fluids outwards from the center of rotation with greater speed and force than if they were just allowed to naturally flow without any additional help from any other forces.
What is open impeller?
An open impeller is a device that consists of a hub with attached vanes and is mounted on a shaft. Open impellers are slightly less efficient than closed or semi-closed impellers.
However, the vane design has a design advantage as blade stresses are lower since the side plate is not fixed to the inlet. In a pump, the fluid enters from the inlet and is directed to the impeller’s eye, where vanes add energy and direct it to the nozzle discharge. A relatively close clearance between vanes and a pump is necessary in order to prevent most of the fluids from flowing back.
You can compensate with wear on the bowl and the edges of the vanes by adjusting this clearance to maintain efficiency over time. More parts are visible, which makes open impellers easier to maintain & inspect for damage. The open impeller can be modified more easily to suit varying needs. They usually operate at a specific range of speeds and are typically faster & easier to maintain. For small pumps and applications that deal with solids, you would usually just use an open impeller. This is because sand locking occurs less frequently when using an open impeller.
What is closed impeller?
A closed impeller is constructed with additional wall sections on the back and front sides of the vanes, giving it greater strength. This also reduces the thrust load on the shaft, increasing bearing life and reliability and reducing shafting costs. Due to this more complex design, closed impellers are more difficult to manufacture and more expensive than open impellers. As the wear ring clearance increases, the efficiency of a closed impeller decreases. Closed impellers work better in a wider range of speeds than open impellers. Used primarily in large-scale pumps and for clear water, these impellers can’t perform effectively with solids. If they get clogged, it becomes difficult to clean them.
When buying a centrifugal pump, we always look for pumps with high efficiency, minimal maintenance and good reliability. One must always consider all these factors, however, one thing that people forget to look at is selecting the right impeller style for your centrifugal pump. Earlier, impellers generally were divided into two categories open and closed. But these days, there is also a third type available. It is called a semi-open impeller. Here are a few differences between the open and closed impeller:
- Closed impellers are the most commonly used impellers in the industry since they can deal with volatile and explosive fluids.
- The closed impeller is initially really efficient, but with time, loses its efficiency as the clearance of the wear ring increases, whereas the efficiency of an open impeller can be maintained through clearance adjustment.
- The pump had to be disassembled when it has a closed impeller to check the status of the wear rings. In an open impeller, no pump disassembling is necessary.
- An open impeller is less likely to get clogged and even if it does, it is easier to clean whereas in a closed impeller, if stringy material or solids are pumped, the impeller can clog and it becomes really difficult to clean them.
- The internal parts of a closed impeller are hidden hence it is difficult to cast and inspect for flaws whereas in an open impeller, all the parts are visible. It thus becomes easy to inspect for damage.
- The design of a closed impeller is more complicated and expensive since the additional wear rings are needed while the open impeller is less costly to build.
- You cannot easily modify a closed impeller so as to improve its performance. While the vanes can be easily cut to improve the capacity in an open impeller.
- In a closed impeller, speed choices are limited. But you have a wide range of specific speed, choice is an open impeller.
As we just saw, there are very specific benefits and pitfalls in both the types of impellers. But it depends on the kind of application you are buying the pump for. Would you think about buying a car that has a poor mileage? No, right? Similarly, when buying a pump if you keep the above mentioned points in mind, you can surely make the best decision without any regrets in the future.
Recent Posts
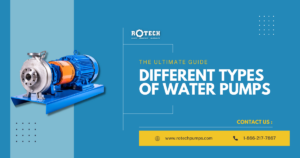
A Comprehensive Guide to Types of Water Pumps and Their Applications
Introduction Water pumps are indispensable
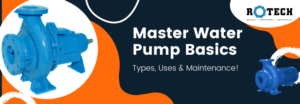
The Complete Guide to Water Pumps: Types, Uses, and Maintenance
Water is life, and the
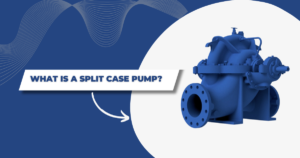
Comprehensive Guide to Split Case Pumps
Split case pumps are a