Flow rate is a crucial parameter when it comes to understanding and operating centrifugal pumps effectively. Centrifugal pumps are widely used in various industries to transport fluids by converting rotational energy into hydrodynamic energy. They find applications in processes such as water supply, wastewater treatment, oil and gas, chemical processing, and more. To comprehend the principles behind centrifugal pump flow rate, it is important to explore its definition and significance within this context.
Centrifugal Pump Flow Rate: Key Concepts
A. Definition of Flow Rate: Flow rate refers to the volume of fluid passing through a system per unit of time. In the context of centrifugal pumps, it represents the amount of fluid being discharged by the pump in a given time period. Flow rate is typically measured in units such as gallons per minute (GPM) or cubic meters per hour (m³/h).
B. Significance of Flow Rate in Centrifugal Pumps: Understanding flow rate is essential for several reasons. Firstly, it determines the pump’s capacity to deliver the required amount of fluid to the intended destination. Secondly, flow rate affects the pump’s efficiency, as variations from the design point can lead to inefficiencies and increased energy consumption. Additionally, flow rate plays a crucial role in system design, selection of the appropriate pump, and maintenance of the system’s operational parameters.
Factors Affecting Centrifugal Pump Flow Rate
A. Pump Design and Impeller Characteristics:
The design of the pump, particularly the impeller, significantly influences the flow rate. Impeller design parameters such as the number of blades, blade angle, and impeller diameter impact the pump’s performance and its ability to generate the desired flow rate.
B. Pump Speed and Impeller Diameter: The rotational speed of the pump, measured in revolutions per minute (RPM), and the impeller diameter are directly related to the flow rate. Higher pump speeds and larger impeller diameters generally result in higher flow rates, assuming other factors remain constant.
Factors Affecting Centrifugal Pump Flow Rate
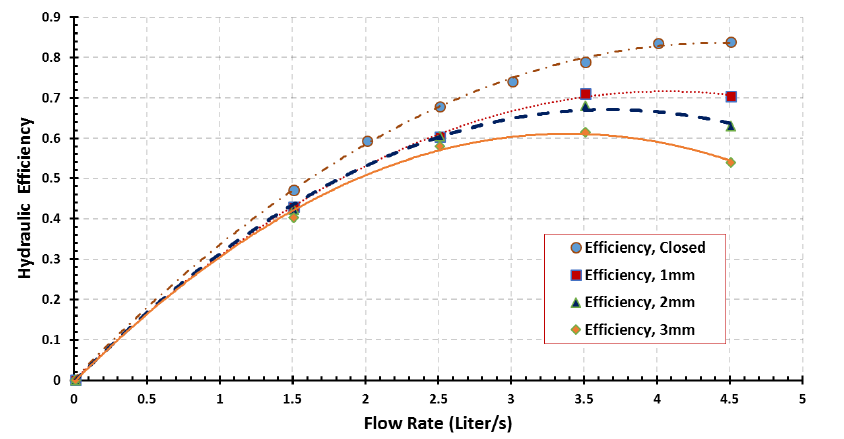
C. System Resistance and Head Loss: The resistance offered by the system, including pipes, valves, fittings, and other components, creates a head loss. Increased system resistance leads to a decrease in the flow rate. Understanding the system’s hydraulic characteristics and minimizing head losses are crucial for achieving the desired flow rate.
D. Viscosity of the Fluid: The viscosity of the fluid being pumped affects the flow rate. Higher viscosity fluids require more power to achieve the desired flow rate due to increased friction losses. Pump selection and system design must consider the fluid’s viscosity to ensure optimal performance.
E. Cavitation and NPSH: Cavitation occurs when the pressure at the impeller inlet drops below the vapor pressure of the fluid, causing the formation of vapor bubbles. This phenomenon can adversely affect the flow rate and pump performance. Net Positive Suction Head (NPSH) is a critical parameter that ensures the prevention of cavitation. Insufficient NPSH can result in decreased flow rates and damage to the pump.
Centrifugal Pump Flow Rate Formula
A. Understanding the Basic Formula: The flow rate (Q) of a centrifugal pump can be calculated using the formula: Q = (π * D^2 * n * H) / (4 * g), where D represents the impeller diameter, n represents the pump speed (RPM), H represents the head, and g represents the acceleration due to gravity.
B. Components of the Formula:
Q: Flow Rate, measured in the desired units (GPM, m³/h, etc.), represents the fluid volume delivered by the pump per unit of time.
D: Impeller Diameter, measured in the same units as the pump dimensions represents the size of the impeller, which affects the pump’s ability to generate flow.
n: Pump Speed (RPM), represents the rotational speed of the pump, which influences the flow rate.
H: Head, measured in units of length (feet, meters, etc.), represents the energy imparted to the fluid by the pump, determining its ability to overcome system resistance and achieve the desired flow rate.
g: Acceleration due to gravity, a constant value used to convert the units of the formula to match the desired flow rate units.
C. Example Calculation using the Formula: Let’s consider an example to illustrate the calculation of flow rate using the formula
RPM | Impeller Diameter (m) | Head (m) | Flow Rate (m³/h) |
---|---|---|---|
1000 | 0.4 | 8 | 160 |
1200 | 0.5 | 10 | 250 |
1500 | 0.5 | 10 | 299.42 (Example) |
1800 | 0.6 | 12 | 400 |
Suppose we have a centrifugal pump with an impeller diameter (D) of 0.5 meters, operating at a speed (n) of 1500 RPM, and generating a head (H) of 10 meters.
Assuming the acceleration due to gravity (g) is 9.81 m/s², the calculation would be as follows: Q = (π * 0.5^2 * 1500 * 10) / (4 * 9.81) Q = (3.14 * 0.25 * 1500 * 10) / (4 * 9.81) Q = 11775 / 39.24 Q ≈ 299.42 m³/h
Using a Centrifugal Pump Flow Rate Calculator
A. Overview of Flow Rate Calculators: Flow rate calculators provide a convenient way to determine the flow rate of a centrifugal pump without manual calculations. These tools utilize the flow rate formula and allow users to input the relevant parameters to obtain accurate results quickly.
B. Online Resources and Tools: Various online resources and engineering websites offer flow rate calculators specifically designed for centrifugal pumps. These calculators often provide additional functionalities, such as unit conversions and the ability to compare different pump configurations.
C. Step-by-Step Guide to Using a Calculator:
Input Parameters: Start by entering the required parameters into the calculator, such as impeller diameter, pump speed, head, and gravitational acceleration. Some calculators may also prompt you to specify the fluid properties or select predefined fluid types.
Obtaining the Flow Rate Result: After inputting the necessary parameters, click the calculate button or similar option provided by the calculator. The tool will process the inputs using the flow rate formula and provide the resulting flow rate value in the desired units.
D. Advantages and Limitations of Flow Rate Calculators: Flow rate calculators offer several advantages, including speed, convenience, and accuracy in obtaining flow rate values. They eliminate the need for manual calculations, reducing the potential for human error. However, it’s important to note that calculators rely on the accuracy of the input parameters, and users should ensure the data provided is reliable for precise results.
Practical Applications and Considerations
A. Selecting the Appropriate Pump for Desired Flow Rate: Understanding the flow rate requirements is essential when selecting a centrifugal pump. By considering factors such as system resistance, head, fluid properties, and desired flow rate, engineers can choose a pump that can meet the specified operational needs efficiently.
B. System Design and Optimization: Proper system design plays a significant role in achieving the desired flow rate. Factors such as pipe sizing, minimizing bends and fittings, and selecting appropriate valves contribute to reducing system resistance and optimizing flow rate performance.
C. Maintenance and Troubleshooting: Regular maintenance of centrifugal pumps is vital for ensuring optimal flow rate. Monitoring impeller condition, checking for blockages, maintaining proper lubrication, and addressing performance deviations are crucial for maintaining desired flow rates and extending the pump’s lifespan.
D. Real-worldExamples and Case Studies: Real-world examples and case studies can provide practical insights into centrifugal pump flow rate applications. These may include scenarios where flow rate requirements were met successfully, challenges encountered and resolved, and the impact of flow rate on overall system performance.
Conclusion:
Understanding the centrifugal pump flow rate is crucial for efficient pump operation and system design. Engineers and operators can ensure optimal pump performance by grasping the key concepts, factors influencing flow rate, the flow rate formula, and utilizing flow rate calculators. Selecting the appropriate pump, considering system design and optimization, and implementing proper maintenance practices are essential for achieving and maintaining desired flow rates. By delving deeper into the subject and exploring real-world examples, individuals can further enhance their understanding of centrifugal pump flow rate and its significance in various applications.
Recent Posts
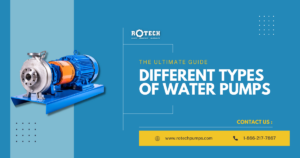
A Comprehensive Guide to Types of Water Pumps and Their Applications
Introduction Water pumps are indispensable
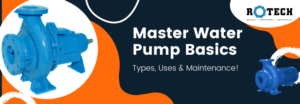
The Complete Guide to Water Pumps: Types, Uses, and Maintenance
Water is life, and the
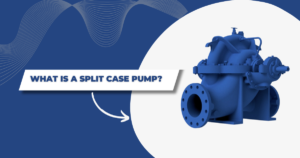
Comprehensive Guide to Split Case Pumps
Split case pumps are a