A centrifugal pump is a mechanical device designed to transport fluids by converting rotational energy from an impeller into kinetic energy. This kinetic energy then converts into pressure, resulting in the movement of the fluid.
Importance of centrifugal pumps in various industries
Centrifugal pumps plays a vital role in a wide range of industries, including oil and gas, chemical processing, water treatment, agriculture, and many others. They are essential for tasks such as transferring liquids, circulating coolant, boosting water pressure, and maintaining industrial processes.
Explore the advantages and disadvantages of centrifugal pumps, providing a comprehensive understanding of their benefits and limitations in different applications.
Advantages of Centrifugal Pumps
High-Efficiency
Centrifugal pumps are designed with impellers that create a centrifugal force, which imparts energy to the fluid. This hydraulic design allows for efficient fluid transfer with minimal energy losses.
Due to their high efficiency, centrifugal pumps require less power consumption compared to other types of pumps. This results in significant energy savings, reducing operational costs and environmental impact.
Wide Range of Applications
Centrifugal pumps find applications in numerous industries, including water supply and treatment, irrigation, chemical processing, HVAC systems, power generation, and more. Their versatility makes them suitable for various fluid transfer tasks.
Simple and Compact Design
It feature a simple design consisting of an impeller, a casing, and inlet/outlet connections. This simplicity makes them easier to manufacture, install, and maintain.
The compact size of centrifugal pumps allows for easy installation in confined spaces. They require less floor area, making them suitable for applications where space is limited, such as onboard ships or in compact industrial facilities.
Ability to Handle Different Pressures
Centrifugal pumps can handle both low and high-pressure operations. By adjusting impeller size, rotational speed, and design features, centrifugal pumps can be optimized to meet specific pressure requirements, offering flexibility in different applications.
Low Maintenance Requirements
Centrifugal pumps are known for their robust construction and reliability. They are designed to handle demanding operating conditions, including continuous operation and handling a wide range of fluids.
Due to their sturdy design and reliable operation, centrifugal pumps require minimal maintenance. This translates into reduced downtime, increased productivity, and cost savings for industries relying on these pumps.
Disadvantages of Centrifugal Pumps
Limited Ability to Handle Viscous Fluids
Centrifugal pumps are primarily designed for low to medium-viscosity fluids. As the viscosity of the fluid increases, the pump’s efficiency decreases, leading to reduced performance and potential issues.
When handling viscous fluids, centrifugal pumps may experience decreased flow rates, reduced head pressures, and increased power consumption. This limitation requires careful consideration when selecting pumps for applications involving viscous fluids.
Sensitivity to Cavitation
Cavitation occurs when the pressure within the pump drops below the vapor pressure of the fluid, leading to the formation and subsequent collapse of vapor bubbles. This can cause damage to the impeller and other pump components.
Cavitation can result in erosion, reduced pump efficiency, and increased vibration and noise levels. To prevent cavitation, measures such as proper pump selection, system design, and the use of cavitation-resistant materials can be employed.
Costly for High-Pressure Applications
Centrifugal pumps have limitations when it comes to handling high-pressure applications. As the required discharge pressure increases, more stages or specialized pumps are necessary, leading to higher costs.
To achieve high-pressure operation, centrifugal pumps may require additional equipment such as booster pumps or multistage pumps. These additions can increase capital and operational expenses.
Complex Control Systems
Centrifugal pumps often require sophisticated control systems to monitor and optimize their performance. These systems involve monitoring variables such as flow rate, pressure, and power consumption to ensure efficient operation.
Operating and maintaining advanced control systems requires knowledgeable personnel who can interpret data, make adjustments, and troubleshoot issues. Skilled operators are essential for achieving optimal pump performance.
Conclusion
Centrifugal pumps offer high efficiency, a wide range of applications, a simple and compact design, and low maintenance requirements. They are energy-efficient, versatile, and reliable tools for fluid transfer in various industries.
While centrifugal pumps have many advantages, they also have limitations. They may struggle with viscous fluids, are sensitive to cavitation, can be costly for high-pressure applications, and require complex control systems. However, these disadvantages can be managed through careful pump selection, system design, and regular maintenance.
Despite their limitations, it remain highly effective and significant in fluid handling applications across industries. With proper understanding, selection, and maintenance, centrifugal pumps continue to play a crucial role in ensuring fluid transport and maintaining industrial processes efficiently and reliably.
Recent Posts
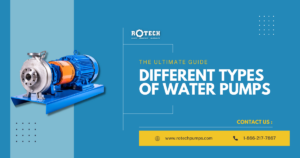
A Comprehensive Guide to Types of Water Pumps and Their Applications
Introduction Water pumps are indispensable
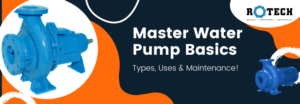
The Complete Guide to Water Pumps: Types, Uses, and Maintenance
Water is life, and the
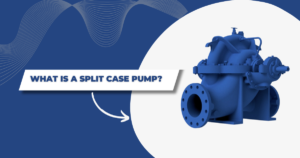
Comprehensive Guide to Split Case Pumps
Split case pumps are a