At first glance, pumps can seem like one complicated topic with many subtopics that all require attention. However, they are actually quite simple if broken down into their most basic parts: suction and elevation. These two actions combine to create a complete pump system capable of transferring fluids either up or down in pressure environments. Pumps are designed very differently depending on what they are used for, how they affect people, and how they work.
These ANSI pumps are available in a variety of constructions and styles. The following is a description of the most common types that are used for industrial, commercial, and residential applications. There are four main types of pumps: centrifugal, positive displacement, hydraulic, and submersible. They differ in how they work to move contaminants by creating force or suction within a pumping chamber to push fluids around or pull them from the source. To learn more about the different types of centrifugal pumps available today, continue reading this post by Rotech!
Process Pumps: Know More Here
A process pump is an instrument that operates on the principle of creating a vacuum. For this reason, it can be used to create fluid flow. The use of process pumps is widespread and common in many different industries, as a way to ensure that fluids are moving properly and to prevent issues like fires or contamination. There are several industries that make use of process pumps, and each of these industries has a reason for using them. Process pumps are used in industrial processes, in labs, and even to aid those suffering from illness.
Process Pumps & Industrial Processes
Industrial processes have several different types of different process pumps that are used for various operations. Many of the process pumps that are used in industrial settings are able to handle large amounts of pressure, as the overall pressure within the system is typically higher than in normal home settings. Process pumps in an industrial setting can be used to move a variety of materials, but they can also be used to create areas where no fluid is present.
If you are looking to find new and better ways to pump liquids, then consider depending on a centrifugal process pump. Centrifugal pumps do more than just push liquid up into the pipes. They offer many benefits over the traditional pipe and valve-type pumps like:
- Less pressure drop in pipelines
- Reduced energy consumption for pumping high water volumes as well as low ones
- The ability to handle rough media such as sand or gravel without damaging components of the pump itself and so much more!
Self Priming Trash Pumps: What Is It?
Self priming trash pumps are used in a wide variety of different applications to pump liquids from various containers that cannot be reached with a solid shaft. It includes recycling units, chemical tanks, marine vessels, and so on. They are generally reliable when positioned in the liquid for which they were designed; in other cases where you must choose between an air-primed unit or a self-primed model, the latter should be your choice. The air pressure will do most of the work for you and make it easier to handle your liquid by turning it into foam before pumping.
When Should You Go For A Self Priming Trash Pump?
In comparison to an air-primed unit that works on the positive displacement principle, the self-primer is a centrifugal pump. Its function is based on air cavitation and centrifugal force instead of a small pump that displaces air. The actual capacity of a self-priming unit is therefore significantly higher than that of an air-primed model. The self priming trash pumps also tend to be more efficient and offer lower installation costs compared to some other models on the market. There are also many variants available with varying degrees of compatibility with different liquids and nozzles, so make sure you choose one that’s best suited for your specific application.
End Suction Pumps: Start to Know About It
End suction pumps are primarily used in the sanitary and food processing industries, where they are often found in high-volume operations. As a result, these pumps have some unique advantages when it comes to performance, use, and maintenance. As mentioned, end suction pumps are very commonly used in high-volume food or sanitation applications. When it comes to these industries, the efficiency of a pump is key. End suction pumps can generally handle higher flow rates than similarly sized centrifugal or diaphragm pumps. This means they can move more products in less time and with less energy—saving you energy costs and increasing your efficiency.
- Because the discharge of an end suction pump is located at the bottom, some manufacturers make them with a quick-disconnect coupling, making them easy to remove for cleaning.
- End suction pumps maintain constant resistance pressure at the discharge point with pumping action;
- Higher capacities at a constant pressure differential;
- The plugged impeller can be removed without removing any piping or instrumentation;
- Installed below ground level or remote from contamination sources.
Vertical Multistage Pumps: Let's Get It Straight
For those unfamiliar with the terminology, “multistage” refers to the use of two or more pumps in sequence. When vertical multistage pumps are used for irrigation purposes, this configuration results in a greater volume of water being delivered downstream, which is especially desirable during periods of prolonged dry weather. Given the wide range of standard vertical multistage pump models on offer today, it’s likely that there will be a particular model that will best suit individual needs. With this in mind, one of the main factors to consider when making a decision about which pump to purchase is the flow rate it can produce.
The benefits of vertical multistage pumps can be summarized as follows:
- They’re ideal for continuous high-flow applications (e.g., irrigation)
- They require less winding area than horizontal multistage because they’re compact and vertical
- Their performance is not restricted by head pressure or total nozzle energy when compared to other configurations
- The configuration minimizes water losses due to the transition from one pump to another.
What Is Your One-Stop Solution?
Rotech manufacturers and suppliers offer many different designs to meet the needs of industrial applications. By using a variety of different technology and new designs, your pump will be more powerful, efficient, and reliable than ever. Pumps manufactured by Rotech are well-suited for industry use and have been recognized by the many years of experience that have gone into their design. Contact us today to learn more about how we can help make your pump the most effective and efficient model available.
Recent Posts
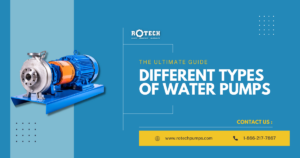
A Comprehensive Guide to Types of Water Pumps and Their Applications
Introduction Water pumps are indispensable
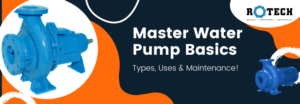
The Complete Guide to Water Pumps: Types, Uses, and Maintenance
Water is life, and the
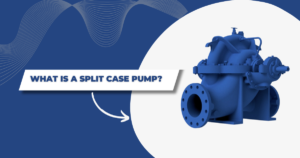
Comprehensive Guide to Split Case Pumps
Split case pumps are a