Rotech isn’t all about manufacturing efficient pumping systems. We also consult you on comprehensive pumping solutions and offer you a quick turnaround on inquiries and support. Rotech has an experienced team of engineers. It is involved in thorough research and development to design & develop new products and find efficient ways to enhance the performance of pumping systems. Rotech also has an in-house pump testing facility and can customize pumps to meet customer requirements. Rotech strives to provide the best quality products at competitive prices with minimum lead time. We have been continuously developing new and effective product lines.
All industries, big & small, need an effective and efficient pumping system. Better & consistent performing pumping systems increase convenience and help overcome day-to-day challenges in industries. Engineers only focus on efficiency while designing the pumps. But a lot of factors affect the consistency of performance in time. Factors such as aging, improper maintenance, miscalculations while installation, and selecting the wrong specifications or a wrong model can all lead to decreased pumping efficiency. These factors should get avoided to achieve desired goals and maintain a step forward in the competition. In this article, Rotech, the manufacturer of efficient process pumps & end suction pumps, will tell how to increase the performance of the pumping systems.
1) Perform Routine Maintenance/Monitoring
Regular maintenance combined with continuous monitoring can yield better results. It is of utmost importance to increase the efficiency and longevity of the pumping system. Regular monitoring can aid in the early detection of problems that are difficult to find and avoid extreme damage to the system.
You can avoid damaged impellers, reduced suction, clogged pipes, and blockage in pumps. Timely replacement of worn parts results in greater pump efficiency. Pumps work best when valves fit properly or when component clearance is within the manufacturer’s specification. In the case of corrosive media, periodically flush pumps with clean water or other acceptable media per the manufacturer’s guidelines.
Routine maintenance includes:
- Impeller repair or replacement, if required
- Bearing inspection, lubrication, or replacement, if required
- Packing seals inspection or replacement if required
- Mechanical seals inspection or replacement, if required
- Pump and motor alignment inspection
2) Prevent Oversizing
Higher performance in terms of flow and pressure requires the motor to run at higher power. An oversized pump uses more energy than necessary. Oversizing the pump during specification commonly attracts uncertainties in the process. Know the limits of the pump. Wearing out of internal components of the pump, such as impellers, valves, gears, and more can cause a loss in efficiency. So make sure you get the correctly designed pump for your application.
Properly size the pump for your application. In case of a new and unique application, prevent oversizing and overdesigning. Determine the required flow rate and discharge pressure to avoid waste and inefficiency.
3) Utilize Innovative Methods
Consider quick, cost-effective, and innovative methods to increase the performance of the pumping systems. Impeller trimming is one such method to reduce the produced pressure. It could be one of the most energy-efficient and cost-effective ways. You can utilize other things, such as a suction stabilizer and discharge pulsation dampeners.
Suction stabilizers reduce pressure inconsistencies and decrease the wearing out of valves and diaphragms. They act as accumulators and reduce the energy required to pull fluid into the pump. The pulsation dampeners ensure a smooth and consistent fluid flow. They remove pulsating flows from reciprocating-type positive displacement pumps, which results in reduced pipe vibration and a longer seal and gasket life.
Use gauges to monitor the pump’s performance. They can get used for both sides of the pump – the suction & discharge sides. You can determine the blockages, low discharge pressure, and other system discrepancies. Gauges can help you establish control limits and trigger early warnings to sustain a better pumping performance.
4) Avoid Unnecessary Usage of Pumps
It might not come to your attention how often pumps are in operation without any purpose because of a lack of control. Implement control systems to control and switch off pumps in case of inactivity. Train the operators of the pumps well who can report and avoid such incidents.
A responsive and well-trained operator is crucial for increasing the performance of the pumps. You can ensure the utmost efficiency & performance of the pumping systems through routine maintenance & monitoring conducted by trained staff members. They report problems with pressure or flow rate and commence necessary remedies.
Rotech has become much more than a pump company through the years. We consult you with solutions to increase the efficiency of your pumping systems. Our aim is to become a valuable resource for our customers and help them make the most of their pumps.
Rotech is a leading manufacturer and supplier of ANSI process pumps, end suction pumps, vertical multistage pumps, and more. We are ready to serve you with efficient pumping systems and effective pumping solutions according to your requirements.
Recent Posts
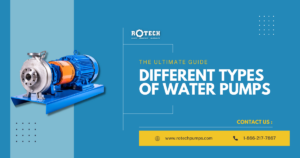
A Comprehensive Guide to Types of Water Pumps and Their Applications
Introduction Water pumps are indispensable
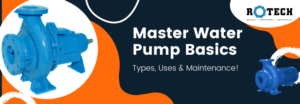
The Complete Guide to Water Pumps: Types, Uses, and Maintenance
Water is life, and the
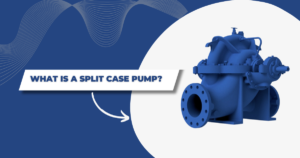
Comprehensive Guide to Split Case Pumps
Split case pumps are a