End suction pumps are a vital component in various industries, serving functions from water supply to wastewater management, heating, cooling, and more. Their proper installation and maintenance are critical to ensure smooth operations, minimize downtime, and extend the life of the equipment. This comprehensive guide explores the key aspects of installing and maintaining end suction pumps, from safety precautions to troubleshooting common issues.
Understanding End Suction Pumps Definition and Basic Components
End suction pumps, also known as ES pumps, are centrifugal pumps designed with a single inlet and a single outlet. They are known for their simple design, which consists of key components such as the impeller, casing, shaft, and motor. Understanding these components is essential before diving into installation and maintenance procedures.
- Impeller: The impeller is the rotating component responsible for generating the pump’s flow. It’s essential to comprehend its design and function as it affects the pump’s performance.
- Casing: The casing surrounds the impeller and directs the flow of fluid. Different casing designs influence the pump’s efficiency and applications.
- Shaft: The shaft connects the impeller to the motor. Proper alignment and maintenance of the shaft are critical for the pump’s longevity.
- Motor: The motor provides the power necessary to drive the impeller. The pump’s performance relies on the motor’s specifications and proper coupling with the impeller.
Types of End Suction Pumps
End suction pumps come in various types to suit different applications. Understanding these types helps in selecting the right pump for your needs and performing tailored maintenance.
- Close-Coupled End Suction Pumps: These pumps have the motor and pump mounted on a common shaft, offering a compact design suitable for many applications.
- Base-Mounted End Suction Pumps: These pumps have a separate baseplate for the motor and pump, offering flexibility in installation and maintenance.
- Vertical Inline End Suction Pumps: These pumps have a vertical configuration, making them suitable for applications with space constraints.
Common Applications
End suction pumps find applications in a wide range of industries:
- Water Supply: Municipal water distribution, well water pumping, and booster systems.
- Heating and Cooling: HVAC systems, chiller circulation, and boiler feed.
- Wastewater Management: Sewage treatment plants, drainage, and effluent pumping.
- Industrial Processes: Chemical processing, food and beverage production, and manufacturing.
- Agriculture: Irrigation, crop spraying, and livestock operations.
Safety Precautions
Before diving into installation and maintenance procedures, it’s crucial to prioritize safety to prevent accidents and injuries.
Personal Protective Equipment (PPE)
- Eye Protection: Safety goggles or face shields to protect against splashes or flying debris.
- Hand Protection: Gloves appropriate for the task, such as chemical-resistant gloves for handling corrosive fluids.
- Footwear: Safety boots with steel toes to protect against heavy objects.
- Hearing Protection: Earplugs or earmuffs for noisy environments.
- Respiratory Protection: Dust masks or respirators if working in dusty or hazardous environments.
Safety Guidelines for Installation and Maintenance
- Lockout/Tagout (LOTO): Implement LOTO procedures to prevent accidental startup of equipment during maintenance.
- Confined Spaces: Follow confined space entry protocols when working in enclosed pump rooms or tanks.
- Chemical Handling: If handling hazardous fluids, follow appropriate chemical safety protocols, including proper ventilation and the use of appropriate personal protective equipment (PPE). Ensure that Material Safety Data Sheets (MSDS) are readily available for reference.
- Electrical Safety: When working with electrical components, follow electrical safety guidelines. Turn off power sources before maintenance and use lockout/tagout procedures. Inspect electrical wiring and connections regularly for signs of wear or damage.
- Lifting and Rigging: Use proper lifting equipment and techniques when handling heavy pump components. Ensure that lifting hooks, slings, and chains are in good condition and appropriately rated for the load.
- Hot Work: If welding or other hot work is necessary, take fire safety precautions, such as having fire extinguishers nearby and ensuring a fire watch is in place.
- Safety Training: Ensure that all personnel involved in installation and maintenance have received adequate safety training, including first aid and emergency response procedures.
Handling Hazardous Materials (if applicable)
- Chemical Compatibility: Verify the compatibility of the pump materials with the fluid being handled to prevent corrosion or damage.
- Spill Response: Have a spill response plan in place and appropriate spill containment and cleanup materials on hand.
- Ventilation: Ensure proper ventilation in areas where potentially harmful fumes or gases may be present.
Installation Procedures
Site Preparation
- Location Selection: Choose an appropriate location for the pump, considering factors such as accessibility, proximity to the fluid source, and environmental conditions.
- Foundation and Baseplate Considerations: Ensure a solid foundation that can support the weight of the pump and motor. Properly align the baseplate with the foundation.
Pump Assembly
- Connecting the Motor: Follow manufacturer guidelines for aligning and connecting the motor to the pump. Use appropriate couplings and ensure they are properly tightened.
- Aligning the Pump and Motor Shafts: Precise alignment is crucial for the pump’s efficiency and longevity. Use alignment tools and techniques to achieve the correct alignment.
- Properly Mounting the Pump: Securely mount the pump on its baseplate, ensuring it is level and well-supported. Use shims as needed for precise alignment.
Piping and Connections
- Suction and Discharge Piping: Properly size and install suction and discharge piping to minimize friction losses and ensure smooth flow. Use appropriate gaskets and seals.
- Check Valves and Isolation Valves: Install check valves to prevent backflow and isolation valves for easy maintenance and repair. Ensure they are correctly positioned and labeled.
Electrical Connections
- Wiring the Motor: Follow the motor manufacturer’s wiring diagram and ensure proper electrical connections. Use conduit and wire of the appropriate size and insulation rating.
- Electrical Safety Measures: Install circuit breakers, disconnect switches, and overload protection devices as required by electrical codes and regulations.
Commissioning
Initial Startup Procedures
- Prime the Pump: Ensure the pump is properly primed with the fluid to prevent dry running during startup.
- Venting: Remove air from the pump and suction piping to ensure optimal performance.
Performance Testing
- Flow Rate and Pressure Testing: Measure and verify the pump’s flow rate and pressure against design specifications.
- Vibration Analysis: Check for abnormal vibrations that may indicate misalignment or other issues.
Adjusting Pump Settings
- Impeller Adjustment: If applicable, adjust the impeller settings to achieve the desired flow and pressure.
Troubleshooting Common Startup Issues
- Cavitation: Identify and address cavitation issues, which can damage the pump and reduce efficiency.
- Excessive Noise: Investigate and resolve any unusual noises during startup.
Maintenance Procedures
Regular Inspection
- Visual Checks: Perform visual inspections regularly to identify leaks, corrosion, and other issues.
- Monitoring Vibrations and Temperatures: Use vibration analysis tools and temperature sensors to detect abnormalities.
Lubrication
- Bearing Lubrication: Lubricate bearings according to the manufacturer’s recommendations.
- Seal Lubrication: Ensure seals are adequately lubricated to prevent leaks.
Seal and Gasket Maintenance
- Inspect Seals: Regularly check seals for wear and replace them as needed.
- Gasket Inspection: Inspect gaskets for signs of deterioration or leaks.
Impeller and Casing Inspection
- Clean Impeller and Casing: Remove debris and buildup from the impeller and casing to maintain efficiency.
Bearing Maintenance
- Bearing Inspection: Check bearing condition and replace if necessary.
- Bearing Alignment: Ensure proper bearing alignment to prevent premature wear.
Alignment Checks and Adjustments
- Shaft Alignment: Periodically check and adjust shaft alignment to maintain optimal pump performance.
Replacing Worn or Damaged Components
- Component Replacement: Replace worn or damaged components promptly to prevent further damage and downtime.
Troubleshooting
Replacing Worn or Damaged Components
- Cavitation: Understand the causes and effects of cavitation and how to mitigate it.
- Low Flow or Pressure: Identify and address issues leading to reduced flow or pressure.
- Excessive Noise or Vibration: Troubleshoot noise and vibration problems to prevent equipment damage.
- Leakage: Address leaks promptly to prevent environmental hazards and equipment damage.
Diagnostic Techniques
- Vibration Analysis: Use vibration analysis tools to diagnose misalignment and imbalance.
- Pressure and Flow Measurements: Monitor pressure and flow rates to identify performance issues.
- Visual Inspection: Perform thorough visual inspections to detect leaks and wear.
Remedial Actions and Solutions
- Corrective Actions: Take appropriate actions to address identified problems, such as realigning shafts or replacing damaged components.
- Preventive Measures: Implement preventive measures to avoid recurring issues.
Preventive Maintenance
Creating a Maintenance Schedule
- Routine Checks: Establish a schedule for routine inspections, lubrication, and maintenance tasks.
- Predictive Maintenance: Implement predictive maintenance techniques, such as vibration analysis and oil analysis, to anticipate and prevent problems.
Predictive Maintenance Techniques
- Vibration Analysis: Monitor vibration levels to detect early signs of misalignment or imbalance.
- Oil Analysis: Analyze oil samples to identify contamination or wear particles.
Spare Parts Inventory Management
- Inventory Assessment: Maintain an inventory of critical spare parts and assess their condition regularly.
- Replenishment Planning: Plan for the timely procurement of spare parts to minimize downtime.
Environmental Considerations
Fluid Handling and Disposal
- Fluid Compatibility: Ensure that the pump and materials used are compatible with the fluid being handled.
- Fluid Containment: Implement measures to prevent fluid spills and leaks.
- Environmental Regulations: Comply with local environmental regulations for fluid handling and disposal.
Energy Efficiency and Sustainability
- Energy Efficiency: Consider energy-efficient pump designs and motor specifications to reduce energy consumption.
- Sustainability Practices: Explore sustainable practices such as pump system optimization and variable frequency drives (VFDs) for energy savings.
In conclusion, this comprehensive guide covers every aspect of installing and maintaining end suction pumps, from safety precautions to troubleshooting and environmental considerations. By following these guidelines, one can ensure the efficient operation and longevity of their end suction pumps while minimizing downtime and costly repairs.
Recent Posts
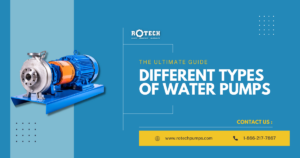
A Comprehensive Guide to Types of Water Pumps and Their Applications
Introduction Water pumps are indispensable
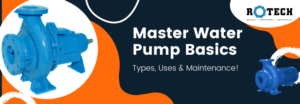
The Complete Guide to Water Pumps: Types, Uses, and Maintenance
Water is life, and the
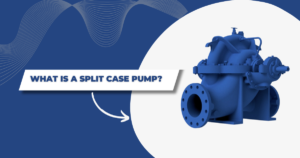
Comprehensive Guide to Split Case Pumps
Split case pumps are a