When we talk about the efficiency of a machine, we are basically referring to its capability to convert one form of energy to another. How well the machine does it becomes efficient. Let’s say we are supplying one unit of energy to a machine and its output is a half unit, we say that the efficiency of the machine is 50%.
The formula for calculating efficiency:
Efficiency % = (output / input) X 100
Coming to our central topic of discussion, centrifugal pumps are highly effective and efficient and are thus in great demand. Digging deep into it, we shall understand more about the efficiency element of these pumps. The centrifugal pump primarily converts mechanical energy into hydraulic energy. Here the flow, velocity, and pressure are also considered. Many medium and large centrifugal pumps offer an efficiency of 75% up to 90%. And the smaller ones usually offer 50% to 70% on average.
How Is Centrifugal Pump Efficiency Attained?
The overall efficiency of a centrifugal pump can be measured by multiplying three individual efficiencies:
- Mechanical Efficiency: It includes the losses in the mechanical seals, stuffing box and bearing frame
- Volumetric Efficiency: It includes losses due to balancing holes and wear rings
- Hydraulic Efficiency: It includes losses in the impeller and the volute plus the losses due to liquid friction. Hydraulic efficiency is the largest factor that decides the overall efficiency of the pump.
When you want to achieve optimum performance and reliability in a centrifugal pump, you must operate the pump close to its BEP (best efficiency point). The BEP is the most stable and suitable operating point for a centrifugal pump. At the best efficiency point, the hydrodynamic unbalanced load of the centrifugal pump is at its minimum. Basically, when a pump operates at a point that is far away from the actual BEP, it results in an overall increase in hydrodynamic unbalanced load. This in turn affects the performance, reliability and efficiency of the centrifugal pump. So the main question is when do we experience maximum unbalanced load? Through experience and experiments, we found that at the shutoff point, an unbalanced load is at its peak, so it’s advised to increase the efficiency of the pump. You must avoid the long-term operation of the pump when it is running near the shutoff point.
There are various conditions that decrease the efficiency of your centrifugal pump that you should be aware of. It includes:
- The heat is generated due to packing.
- Rubbing between wear rings and maintaining impeller clearances.
- Recirculation using a bypass line from the discharge of the pump to the suction.
- Double volute design.
- Throttled discharge valve.
- Corroded internal pump passages that cause fluid turbulence.
- Obstacles, hindrances or any sort of restrictions inside the piping passages might include foreign particles or dirt.
- Over lubricated bearings.
If you are searching for centrifugal pumps with maximum efficiency, you might want to browse through a wide range of pumps offered by Rotech Pumps. Excellent quality equipment and after-sales service are the key elements owing to the huge success of Rotech Pumps.
Recent Posts
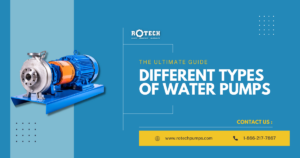
A Comprehensive Guide to Types of Water Pumps and Their Applications
Introduction Water pumps are indispensable
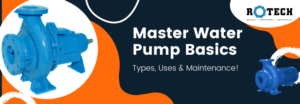
The Complete Guide to Water Pumps: Types, Uses, and Maintenance
Water is life, and the
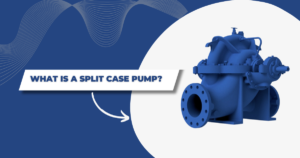
Comprehensive Guide to Split Case Pumps
Split case pumps are a