End suction pumps are widely used in various industries for their efficient fluid transfer capabilities. Understanding the advantages and disadvantages of these pumps is crucial for making informed decisions regarding their implementation. This article will delve into the benefits and drawbacks of end suction pumps, allowing readers to assess their suitability for specific applications.
Advantages of End Suction Pumps:
- Reliable and Durable Performance: End suction pumps have a proven track record of reliability and durability. They are known for their robust construction, which ensures consistent performance even in demanding operating conditions. This reliability factor makes them a popular choice across industries.
- Wide Range of Sizes and Designs: End suction pumps are available in a diverse range of sizes and designs, offering flexibility to match specific application requirements. Whether it’s a small-scale operation or a large industrial project, there is a suitable end suction pump available to meet the desired specifications.
- Efficient Fluid Transfer with High Efficiency: These pumps are designed for efficient fluid transfer, offering high efficiency in terms of energy consumption. They can effectively handle a wide range of flow rates while maintaining performance consistency. Their ability to transfer fluids with minimal energy wastage contributes to cost savings in the long run.
- Ease of Installation and Maintenance: It is relatively easy to install and maintain. Their simple design and modular construction make installation straightforward. Additionally, routine maintenance tasks such as inspections, repairs, and part replacements can be performed with ease, minimizing downtime and associated costs.
- Interchangeable Parts for Convenience: It is designed with interchangeable parts, facilitating quick and convenient maintenance and repairs. This feature allows for efficient troubleshooting and replacement of components, reducing downtime and maximizing operational efficiency.
- Compact Design for Space Optimization: One of the key advantages of end suction pumps is their compact design, which enables them to occupy minimal space. This makes them suitable for installations where space is a constraint. Their small footprint ensures flexibility in plant layout and allows for easy integration into existing systems.
- Cost-Effective Compared to Other Pump Configurations: It offers cost-effective solutions for fluid transfer requirements. Their relatively lower initial cost, combined with efficient operation and ease of maintenance, results in reduced lifecycle costs. This cost-effectiveness makes them an attractive choice for applications where budget considerations are paramount.
- Versatility for Various Applications: It is versatile and can be used in a wide range of applications. From HVAC systems, water supply and distribution, irrigation, to general industrial processes, these pumps can handle diverse fluid transfer needs. Their adaptability contributes to their popularity across different industries.
- Minimal Noise during Operation: It is designed to operate with minimal noise emissions. Their quiet operation makes them suitable for applications where noise reduction is important, such as in residential or commercial buildings or noise-sensitive environments.
Disadvantages of End Suction Pumps:
- Limited to Single-Stage Operation: End suction pumps are typically limited to single-stage operation. This means they may not be suitable for applications that require high-pressure pumping or multiple stages of pressure boosting.
- Lower Efficiency for High-Pressure Applications: Compared to multi-stage pumps, end suction pumps may have lower efficiency when it comes to high-pressure applications. If high pressures are required, other pump configurations, such as multi-stage pumps, may be more suitable.
- Possible Cavitation Issues: In certain conditions, end suction pumps may be susceptible to cavitation, which is the formation and collapse of vapor bubbles in the pump. Cavitation can cause damage to the pump and reduce its performance. Proper consideration of operating conditions and implementing measures to prevent cavitation are necessary.
- Reduced Effectiveness with Viscous Fluids: It may experience reduced effectiveness when handling viscous fluids. The higher viscosity of fluids can impact the pump’s efficiency and performance. In such cases, alternative pump types, like gear or progressive cavity pumps, might be more suitable for handling viscous fluids.
- Potential for Higher Power Consumption in Large-Scale Operations: For large-scale operations that require high flow rates, end suction pumps may consume more power compared to other pump configurations. It’s important to consider the energy requirements and operating costs associated with the pump’s power consumption for such applications.
- Not Suitable for Handling Abrasive or Corrosive Fluids without Proper Modifications: Standard-end suction pumps may not be suitable for handling abrasive or corrosive fluids without appropriate modifications. In applications where fluids contain solids or chemicals that can cause damage to pump components, specialized materials or protective coatings may be required.
Conclusion
End suction pumps offer numerous advantages, including reliability, versatility, and cost-effectiveness. However, they may have limitations related to high-pressure applications, viscous fluids, and potential cavitation issues. By carefully considering the specific requirements of the application and conducting a thorough assessment, end suction pumps can be selected and optimized for efficient fluid transfer. Consultation with reputable manufacturers and industry experts like Rotech Pumps can ensure the appropriate selection and successful implementation of end suction pumps in various industries and applications.
Recent Posts
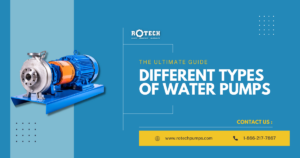
A Comprehensive Guide to Types of Water Pumps and Their Applications
Introduction Water pumps are indispensable
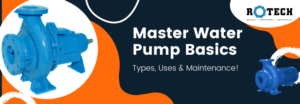
The Complete Guide to Water Pumps: Types, Uses, and Maintenance
Water is life, and the
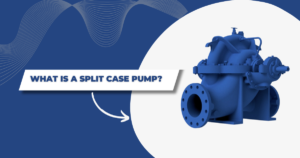
Comprehensive Guide to Split Case Pumps
Split case pumps are a