A self-priming pump is a type of centrifugal pump designed to automatically remove air or gases from the suction side of the pump during the priming process. In traditional centrifugal pumps, the pump casing and impeller must be filled with liquid (primed) before the pump can start pumping effectively. However, self-priming pumps are specifically engineered to overcome this limitation.
Self-priming pumps have a unique design that includes a built-in mechanism or feature to evacuate air from the pump casing and suction line, allowing the pump to create a vacuum and draw in the fluid to be pumped. This makes them particularly useful in situations where the pump is located above the fluid source or where the fluid supply may be intermittent or contain air pockets.
Key features of self-priming pumps include:
- Primed for Air Handling: These pumps are designed to handle air or gas mixed with the fluid, allowing them to maintain their primed state even when air is present in the system.
- Check Valves or Flapper Valves: Self-priming pumps often incorporate check valves or flapper valves in the suction line to prevent the pumped fluid from flowing back and to maintain the primed state.
- Recirculation: Some self-priming pumps use a recirculation system that directs a portion of the pumped fluid back to the pump’s casing during startup, aiding in the priming process.
How Self-Priming Pumps Work
Self-priming pumps work by using a combination of design features and mechanisms to remove air or gases from the pump casing and suction line, allowing the pump to create a vacuum and draw in the fluid to be pumped. Here’s a basic overview of how self-priming pumps work:
- Initial Filling: When the self-priming pump is initially started, the pump casing and impeller are partially filled with liquid. This liquid can come from a priming reservoir, an external source, or through a recirculation system within the pump itself.
- Air Evacuation: As the pump starts to operate, the impeller rotates, creating a centrifugal force that forces the liquid outward. At the same time, the liquid in the impeller’s vanes pushes air toward the pump casing’s discharge or outlet. This air is then expelled through a vent or air release valve.
- Creation of Vacuum: As the air is removed from the pump casing and suction line, a vacuum is created within the pump. This vacuum helps to draw fluid in from the suction line.
- Fluid Inlet: The fluid from the suction line is drawn into the pump casing due to the vacuum created. The fluid fills the void left by the expelled air.
- Fluid Discharge: Once the fluid is drawn into the pump casing, it mixes with the liquid already present and is then pushed by the impeller toward the pump’s discharge outlet.
- Check Valves or Flapper Valves: Many self-priming pumps incorporate check valves or flapper valves in the suction line to prevent the pumped fluid from flowing back into the source during the pumping cycle. These valves maintain the primed state and help ensure that air is not reintroduced into the pump casing.
- Continuous Operation: Once the self-priming pump is successfully primed and fluid is flowing, it continues to operate efficiently. The pump will continue to evacuate any small amounts of air or gases that might be introduced during operation, ensuring that the pumping process remains effective.
It’s important to note that the specific design and operation of self-priming pumps can vary based on the manufacturer and the intended application. Some self-priming pumps may use additional features like recirculation systems, priming chambers, or specialized impeller designs to enhance their self-priming capabilities. Proper installation, maintenance, and monitoring are crucial to ensure the reliable and effective functioning of self-priming pumps.
Types of Self-Priming Pumps
There are several types of self-priming pumps, each designed to suit specific applications and requirements. The following are some common types of self-priming pumps:
There are several types of self-priming pumps, each designed to suit specific applications and requirements. The following are some common types of self-priming pumps:
- Centrifugal Self-Priming Pumps: These are the most common type of self-priming pumps. They use a centrifugal impeller to create a vacuum and draw in the fluid. Centrifugal self-priming pumps are suitable for a wide range of applications, including water transfer, irrigation, and wastewater pumping.
- Trash Pumps: Trash pumps are a type of centrifugal self-priming pump designed to handle fluids with solids, debris, and other abrasive materials. They are commonly used in construction, mining, and municipal applications for pumping slurry, mud, and other heavy-duty fluids.
- Jet Pumps: Jet self-priming pumps use a venturi effect to create suction and draw fluid into the pump casing. They consist of a jet assembly that generates a high-velocity flow of liquid, creating a vacuum and inducing the fluid to enter the pump. Jet pumps are often used in shallow well and domestic water supply systems.
- Diaphragm Self-Priming Pumps: Diaphragm pumps use flexible diaphragms to move fluid through the pump. These pumps can handle fluids with high viscosity, solids, and chemicals. Diaphragm self-priming pumps are commonly used in industrial processes, chemical handling, and wastewater treatment.
- Rotary Vane Self-Priming Pumps: Rotary vane pumps use rotating vanes to create a vacuum and draw in the fluid. They are suitable for handling thin liquids, fuels, and light oils. Rotary vane self-priming pumps are often used in automotive and fuel transfer applications.
- Liquid Ring Self-Priming Pumps: Liquid ring pumps use a rotating liquid ring to create a vacuum and draw in the fluid. They are commonly used in applications where the pumped fluid contains gases or where a continuous, non-pulsating flow is required, such as in the chemical and pharmaceutical industries.
- Peripheral Self-Priming Pumps: Peripheral pumps, also known as regenerative or side-channel pumps, use an impeller with radial blades that channel fluid around the pump casing. This design creates a continuous flow and self-priming capabilities. Peripheral self-priming pumps are suitable for low flow and high-pressure applications.
- Piston Self-Priming Pumps: Piston pumps use reciprocating pistons to move fluid through the pump. They are often used in applications where high pressures are required, such as in pressure washing systems and firefighting equipment.
Each type of self-priming pump has its own advantages and limitations, and the choice of pump depends on factors such as the type of fluid being pumped, the presence of solids or gases, required flow rates, pressure requirements, and the specific application’s demands. Proper selection, installation, and maintenance of the appropriate self-priming pump type are crucial for achieving efficient and reliable pumping performance.
Applications of Self-Priming Pumps:
Self-priming pumps are versatile and find applications in various industries and scenarios where efficient fluid transfer, handling of solids, and reliable operation are essential. Some common applications of self-priming pumps include:
- Wastewater and Sewage Handling: Self-priming pumps are widely used for lifting and transferring wastewater, sewage, and sludge in municipal sewage systems, industrial wastewater treatment plants, and septic systems. Their ability to handle solids and maintain priming makes them valuable in these applications.
- Construction and Dewatering: Self-priming pumps are used to dewater construction sites, excavations, and basements. They can handle water with sediment and debris, making them suitable for pumping out accumulated water from construction projects.
- Irrigation and Agriculture: Self-priming pumps are used for irrigation systems, pumping water from wells or water bodies to supply agricultural fields with water. Their ability to handle variable water sources and intermittent operation is beneficial in agricultural settings.
- Marine and Bilge Pumping: On boats, ships, and other marine vessels, self-priming pumps are used for bilge pumping to remove water that accumulates in the hull. They can handle seawater and prevent flooding.
- Emergency and Flood Control: Self-priming pumps are employed in flood control systems to rapidly remove excess water from areas prone to flooding. They are also used in emergency situations to manage water accumulation.
- Industrial Processes: Self-priming pumps are used in various industrial processes, including chemical transfer, food and beverage processing, and pharmaceutical production. Their ability to handle different fluids and maintain priming is advantageous in these settings.
- Firefighting: Self-priming pumps are used in firefighting equipment to quickly draw water from sources like lakes, ponds, or hydrants. Their ability to self-prime ensures rapid response in emergencies.
- Mining Operations: Self-priming pumps are used in mining for dewatering pits and underground tunnels. They can handle water with solids and ensure effective drainage.
- Oil and Gas Industry: Self-priming pumps find applications in the oil and gas industry for transferring liquids containing gases, crude oil, and refined products.
- Municipal Water Supply: Self-priming pumps can be used in municipal water supply systems to pump water from wells or reservoirs to distribution networks.
- Pulp and Paper Industry: Self-priming pumps are used for handling various fluids in the pulp and paper manufacturing process, including pumping slurry and chemical solutions.
- Agricultural Spraying: Self-priming pumps are used in agricultural spraying equipment to transfer fertilizers, pesticides, and other chemicals from storage tanks to spraying systems.
These applications highlight the versatility of self-priming pumps and their ability to handle diverse fluids, handle solids, and ensure reliable operation even in challenging conditions. Proper selection, installation, and maintenance of self-priming pumps are essential to achieve optimal performance in these various applications.
Conclusion
Self-priming pumps have transformed the way fluids are moved across industries, providing a reliable and efficient solution to the challenges of priming. With their unique mechanisms and versatile applications, self-priming pumps offer practical solutions to scenarios where conventional pumps fall short. As technology continues to advance and new industries emerge, the role of self-priming pumps is set to expand, contributing to a more efficient, reliable, and sustainable future. Whether in water supply, construction, industrial processes, or emergency response, self-priming pumps have become an integral part of modern fluid handling systems, driving progress and innovation in diverse fields.
Recent Posts
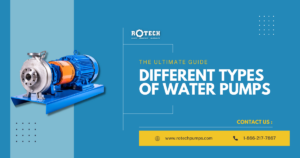
A Comprehensive Guide to Types of Water Pumps and Their Applications
Introduction Water pumps are indispensable
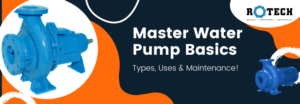
The Complete Guide to Water Pumps: Types, Uses, and Maintenance
Water is life, and the
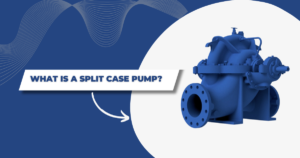
Comprehensive Guide to Split Case Pumps
Split case pumps are a